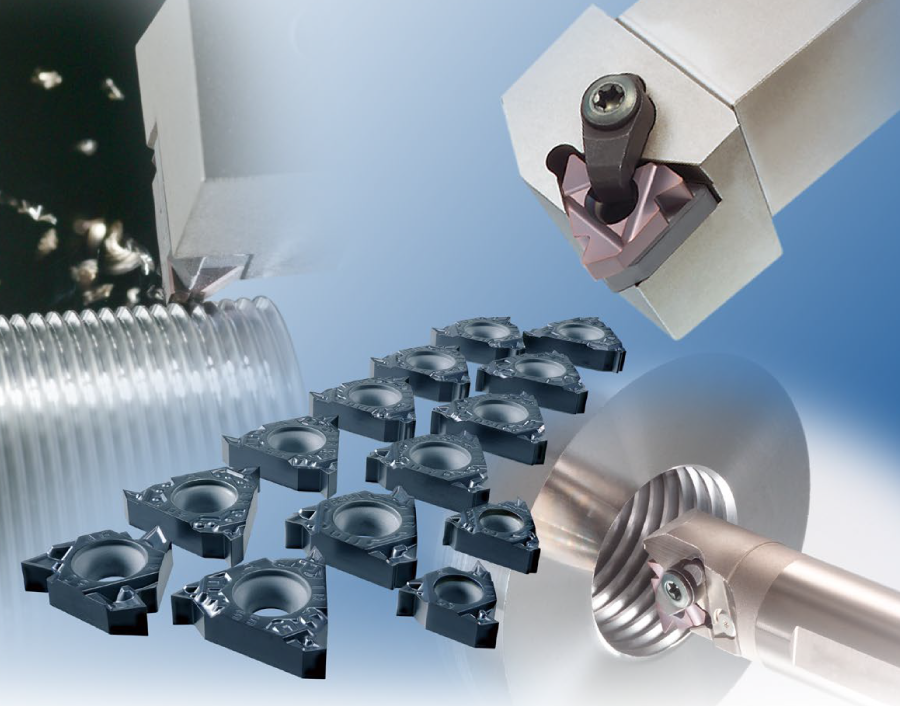
Here is the website URL https://www.wencerl.com. Wencerl is a number one supplier of
Stop Mills: Flexible Resources for Exact Materials Removing
Sq. Finish Mills: Perfect for generating sharp corners and flat-bottomed cavities. Ball Nose Conclude Mills: Great for 3D contouring and sculpting intricate surfaces. Corner Radius End Mills : Blend the characteristics of square and ball nose mills for extra energy and flexibility.Roughing Close Mills: Created for swift material elimination with minimal warmth technology. Ending Finish Mills: Give easy finishes and limited tolerances in delicate operations.
Milling Applications: Vital Parts for Economical Milling Operations
Face Mills: Employed for machining flat surfaces and generating a wonderful complete. Shell Mills: Flexible applications which can be utilized for both of those roughing and ending functions. Slab Mills: Appropriate for removing significant quantities of fabric from the workpiece. Close Mills: Offer flexibility in chopping many supplies and shapes. - Fly Cutters: Give a Charge-powerful Resolution for obtaining a easy area complete.
Tool Holders: Making certain Balance and Precision in Machining
Collet Chucks: Offer large clamping force and are perfect for Keeping compact-diameter equipment. End Mill Holders: Made to securely hold close mills and decrease Resource runout. - Shell Mill Arbors: Accustomed to mount shell mills onto the equipment spindle.
Drill Chucks : Allow for speedy alterations in between drills and other tools.Fast Change Software Posts: Help fast Software changes, lessening downtime in CNC operations.
Precision Cutting Resources: Achieving Large Accuracy in Machining
Carbide Tools: Provide great hardness and dress in resistance for prolonged Instrument lifetime. Cermet Instruments: Present exceptional floor finish and are ideal for superior-pace machining. Significant-Pace Metal (HSS) Resources: Adaptable and value-efficient, well suited for a variety of apps. Ceramic Applications: Effective at withstanding large temperatures and therefore are utilized for really hard material machining. Polycrystalline Diamond (PCD) Applications: Give Excellent have on resistance for machining non-ferrous supplies.
Threading Resources: Creating Interior and External Threads with Precision
Thread Mills: Utilized for creating interior and exterior threads with substantial accuracy. - Faucet Drills: Deliver the right hole sizing for tapping operations.
Die Heads: Allow for fast and precise thread cutting in guide functions. Threading Inserts : Replaceable slicing edges for economical thread manufacturing.Chasers : Used in lathes for slicing threads on cylindrical workpieces.
Drilling Resources: Important for Generating Holes in Different Products
Twist Drills: Generally used for drilling holes in metallic, Wooden, and plastic. - Centre Drills: Utilized to produce a conical gap for correct centering with the workpiece.
Phase Drills: Permit for drilling a number of gap sizes without switching tools. Spade Drills : Ideal for deep gap drilling with higher product removing costs.Gun Drills: Made for precision drilling of deep holes with little diameters.
Turning Tools: Shaping Components with Rotational Movement
Turning Inserts: Replaceable reducing edges for turning operations. Parting Tools: Used to Slice off sections of a workpiece during turning. - Monotonous Bars: Let for inner diameter machining with superior precision.
Grooving Resources : Make grooves and slots from the workpiece.- Knurling Instruments: Create textured styles on cylindrical surfaces for improved grip.
Chopping Instrument Supplies: Selecting the Proper Materials with the Job
High-Speed Metal (HSS): Presents very good toughness and it is ideal for general-reason machining. Cemented Carbide: Gives high hardness and use resistance for extended Device lifetime. Cermet: Combines ceramic and metallic resources for improved surface area complete. Ceramic : Able to withstanding significant temperatures for machining really hard elements.Polycrystalline Diamond (PCD) : Delivers Outstanding put on resistance for non-ferrous product machining.
cutting snips